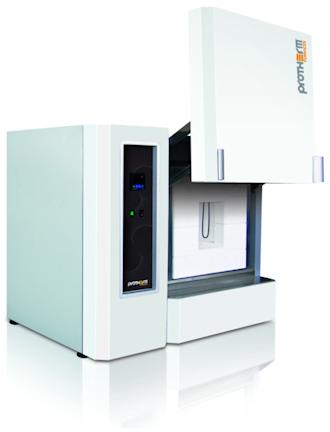
Standard MoS series furnaces cover a range from 1600°C to 1800°C, all of which have front loading for easy operation and double skin construction to maintain a cooler outer case.
Important advantage of the model is that element change is very easy and economic. Furnaces starting from 1800°C use high quality Molybdenum Disilicide heating elements, providing a very long service life.
Galvanized coating covered epoxy painted structure, providing longer life time and aesthetics.
Typical applications for the product is almost all high temperature applications where high level of precision is required; high temperature sintering processes such as Ceramic, Dental and Material Research.
System Features
Vertical counter balanced door
Standard door safety switch
Customized controller option
High-quality fiber material
High level temperature uniformity
Bottom protection, alumina plates on the floor
Standard brick design on the outer skirts of the door and the furnace opening providing protection from possible unwanted damages during loading and unloading.
Table top and Self-Standing design
Standard door safety switch
Customized controller option
High-quality fiber material
High level temperature uniformity
Bottom protection, alumina plates on the floor
Standard brick design on the outer skirts of the door and the furnace opening providing protection from possible unwanted damages during loading and unloading.
Table top and Self-Standing design
High quality heating elements ensuring a long service life
System operation with solid-state-relays
Short heating times
Electrical protection
Working Temperatures of up to 1800°C
Dual skin housing for low external temperatures and high inner temperature stability
Easy replacement of heating elements
Intuitive controller user interface
System operation with solid-state-relays
Short heating times
Electrical protection
Working Temperatures of up to 1800°C
Dual skin housing for low external temperatures and high inner temperature stability
Easy replacement of heating elements
Intuitive controller user interface
Specifications
Model | Maximum Temperature (°C) | Continuous Operating Temperature °C | Inner Dimensions HxWxD (cm) | Inner Volume (liters) | External Dimensions HxWxD (cm) | Approximate Power (kW) | Phase | Supply (V) |
MoS-B 150/1 | 1550 | 1500 | 12x12x9 | 1.3 | 71x51x47 | 1.5 | 1 | 220 |
MoS-B 150/2 | 1550 | 1500 | 14x12x15 | 2.5 | 77x51x51 | 3.3 | 1 | 220 |
MoS-B 160/1 | 1600 | 1550 | 12x12x9 | 1.3 | 71x51x47 | 1.5 | 1 | 220 |
MoS-B 160/2 | 1600 | 1550 | 14x12x15 | 2.5 | 77x51x51 | 3.3 | 1 | 220 |
MoS-B 160/4 | 1600 | 1550 | 14x14x20 | 3.9 | 66x82x52 | 4.4 | 1 | 400 |
MoS-B 160/8 | 1600 | 1550 | 18x18x25 | 8.1 | 70x92x52 | 7.2 | 3 | 400 |
MoS-B 170/2 | 1700 | 1650 | 14x12x15 | 2.5 | 77x51x51 | 3.3 | 1 | 220 |
MoS-B 170/4 | 1700 | 1650 | 14x14x20 | 3.9 | 66x82x52 | 4.4 | 1 | 400 |
MoS-B 170/8 | 1700 | 1650 | 18x18x25 | 8.1 | 70x92x52 | 7.2 | 3 | 400 |
MoS-B 180/2 | 1800 | 1750 | 14x12x15 | 2.5 | 77x51x51 | 3.3 | 1 | 220 |
MoS-B 180/4 | 1800 | 1750 | 14x14x20 | 3.9 | 66x82x52 | 4.4 | 1 | 400 |
MoS-B 180/8 | 1800 | 1750 | 18x18x25 | 8.1 | 70x92x52 | 7.2 | 3 | 400 |
MoS-F 160/8 | 1600 | 1550 | 18x18x25 | 8.1 | 145x58x61 | 7.2 | 3 | 400 |
MoS-F 160/12 | 1600 | 1550 | 24x20x25 | 12.0 | 145x62x61 | 9.0 | 3 | 400 |
MoS-F 160/16 | 1600 | 1550 | 24x22x30 | 15.8 | 145x62x61 | 11.3 | 3 | 400 |
MoS-F 170/8 | 1700 | 1650 | 18x18x25 | 8.1 | 70x92x52 | 7.2 | 3 | 400 |
MoS-F 170/12 | 1700 | 1650 | 24x20x25 | 12.0 | 145x62x61 | 9.0 | 3 | 400 |
MoS-F 170/16 | 1700 | 1650 | 24x22x30 | 15.8 | 145x62x61 | 11.3 | 3 | 400 |
MoS-F 180/8 | 1800 | 1750 | 18x18x25 | 8.1 | 70x92x52 | 7.2 | 3 | 400 |
MoS-F 180/12 | 1800 | 1750 | 24x20x25 | 12.0 | 145x62x61 | 9.0 | 3 | 400 |
MoS-F 180/16 | 1800 | 1750 | 24x22x30 | 15.8 | 145x62x61 | 11.3 | 3 | 400 |
Optional Features
Over-temperature limiter for thermal protection
Adjustable air intake opening in the furnace door
Exhaust air opening in the of the furnace roof
Option of sideways opening door
Observation hole enabling the operator observe the load during the operation
Data logger with the software
Adjustable air intake opening in the furnace door
Exhaust air opening in the of the furnace roof
Option of sideways opening door
Observation hole enabling the operator observe the load during the operation
Data logger with the software
RS422/485 communication
Cooling Fan for faster cooling processes
Jet Fan for faster exhaust of gases
Movable bottom enabling the operator to remove the sample while the furnace is still hot
Quartz element protection for heating elements
Protective gas system and connection
Cooling Fan for faster cooling processes
Jet Fan for faster exhaust of gases
Movable bottom enabling the operator to remove the sample while the furnace is still hot
Quartz element protection for heating elements
Protective gas system and connection